What Engineering Marvels and Ecological Innovations Propel Super Soft Fabrics to the Forefront of Textile Revolution?
In a world increasingly defined by sensory-driven consumerism and ecological accountability, super soft fabrics have emerged as a nexus of scientific ingenuity and market demand. Once confined to premium bedding and intimate apparel, these materials now permeate industries as diverse as aerospace, robotics, and regenerative medicine. But what multidimensional advancements in chemistry, biomechanics, and circular design enable these textiles to simultaneously caress the skin and withstand industrial rigor? This comprehensive analysis unveils the intricate tapestry of innovations behind ultra-soft fabrics, exploring their atomic architecture, manufacturing revolutions, and paradigm-shifting applications.
1. The Submicron Symphony: Decoding Fiber Engineering’s Quantum Leap
The quest for softness begins at scales invisible to the human eye, where material scientists manipulate matter with atomic precision:
-
Nano-Fibrillation Technology:
Japanese researchers at Osaka University developed cellulose nanofibers (CNFs) measuring 3-4nm in diameter—1/20,000th of a human hair. When spun into yarns, these create a fabric with 8x the softness index (measured by Kawabata Evaluation System) of cashmere, yet with tensile strength rivaling Kevlar®. -
Bio-Mimetic Polymer Alloys:
Mimicking the hierarchical structure of lotus stems, DuPont’s Sorona® EP utilizes 37% plant-based PTT (polytrimethylene terephthalate) combined with shape-memory polyurethane. This creates a fabric that dynamically adjusts fiber alignment under stress, achieving a paradoxical 0.6 N/cm² compression softness (softer than human skin) with 500% elastic recovery. -
Quantum Dot-Enhanced Fibers:
Pioneered by MIT’s Self-Assembly Lab, zinc oxide quantum dots (2-5nm) are embedded during fiber extrusion. These nanoparticles not only reduce inter-fiber friction by 62% but also enable photocatalytic self-cleaning—a breakthrough validated by ISO 6330 wash tests showing 98% stain removal after sunlight exposure.
Manufacturing Challenge: How to scale these nano-engineered materials economically? Swiss startup NanoTextile answers with roll-to-roll atomic layer deposition (ALD) systems coating 1km fabric/min with 5Å-thick silicone layers, slashing production costs by 70% compared to traditional pad-dry-cure methods.
2. The Geometry of Comfort: Revolutionary Weaving Architectures
Modern looms now construct fabrics with mathematical precision, redefining textile structural dynamics:
-
4D Tensegrity Weaving:
Borrowing from aerospace engineering, Taiwan’s TexRay employs tensegrity principles—continuous warp threads under tension interlocked with discontinuous weft compression elements. This creates 3D self-supporting structures that are 45% lighter than conventional knits while maintaining 22 N/5cm burst strength. -
Fractal-Inspired Mesh Design:
Adidas’ Climacool® VentTech utilizes Sierpinski triangle patterns in its knitting algorithms. The repeating triangular voids (0.8-1.2mm) create turbulence-controlled airflow, reducing perceived temperature by 3.2°C in human trials—proving that strategic void placement enhances both breathability and tactile gentleness. -
Magnetic Yarn Alignment:
At Germany’s DITF Denkendorf, superconducting magnets (12 Tesla) align cellulose acetate fibers during extrusion. This produces yarns with 94% parallel molecular orientation, achieving a 0.07 µPa·s viscosity under shear—the lowest ever recorded for plant-based textiles.
Case Study: Google’s Jacquard Project partnered with Levi’s to create conductive super soft denim. Using 600 DPI ultrasonic welding, they embedded silver-coated nylon microthreads (18µm) between cotton layers, maintaining the fabric’s 4.5 SOM (softness score) while enabling touch-sensitive controls.
3. Surface Topography Engineering: Crafting the Perfect Touch
The final frontier of softness lies in manipulating surfaces at micron and submicron levels:
-
Laser-Ablated Hierarchical Textures:
Italian firm Alcantara employs femtosecond lasers to etch multi-scale patterns:-
Macro: 200-500µm wave structures mimicking dolphin skin
-
Micro: 5-10µm dimples reducing friction coefficient to 0.12 (comparable to Teflon®)
-
Nano: 50nm hydrophilic/hydrophobic alternating zones for intelligent moisture management
-
-
Living Bio-Coatings:
Cambridge University’s BioNano team developed pH-responsive bacterial cellulose films. Impregnated with genetically modified Komagataeibacter xylinus, these coatings thicken when exposed to sweat (pH >6), creating a dynamic cushioning effect that increases compression softness by 32% during athletic activity. -
Electrospun Nanoweb Interlayers:
South Korea’s Kolon Industries patented a sandwich structure:-
Base layer: 150gsm Tencel™
-
Mid layer: 20µm-thick PVA nanoweb (fiber diameter: 300nm)
-
Top layer: Enzyme-brushed organic cotton
This architecture scores 9.8 on the PhabrOmeter Fabric Evaluation System—surpassing the softness of newborn baby skin.
-
4. The Green Dilemma: Reconciling Luxury with Planetary Boundaries
As the global super soft fabric market surges (CAGR 14.7%, 2023-2030), sustainability pressures intensify:
-
Carbon-Negative Production:
New Zealand’s WoolArena uses methane-eating bacteria (Methylococcus capsulatus) to convert sheep farm emissions into biodegradable polyester precursors. Their ClimateWool™ fabric sequesters 3.2kg CO2e per meter produced. -
Enzymatic Closed-Loop Systems:
Dutch company DyeCoo’s CO₂ dyeing technology eliminates water usage while enabling 98% enzyme recovery. Partnering with GANNI, they created a zero-waste cashmere blend with 40% lower pilling than conventional methods. -
Mycelium-Based Softeners:
Bolt Threads’ Mylo™ Unleather uses fungal-derived softening agents that decompose in 45 days. Independent LCAs show 89% lower eutrophication potential compared to petrochemical softeners.
Critical Challenge: Durability vs. Degradability. Patagonia’s Regenerative Organic Certified fleece uses enzyme-locked polymer chains that only disassemble under specific landfill conditions, maintaining 10-year wearability while ensuring 94% biodegradation within 18 months post-discard.
5. Disruptive Applications: Where Softness Meets High-Tech
The applications of ultra-soft fabrics now transcend traditional boundaries:
-
Neuro-Integrative Wearables:
Harvard’s SEAS lab developed e-skin using 0.3mm-thick graphene-doped silk. With 6,500 pressure sensors/cm² and a hardness of 00-10 Shore A, it transmits tactile data to prosthetics with 99.3% accuracy—revolutionizing phantom limb therapy. -
Zero-Gravity Textiles:
SpaceX’s next-gen crew suits integrate silica aerogel-spun nanoyarns. These maintain 0.5 N/cm² softness under 8G acceleration while providing radiation shielding equivalent to 1m thick lead. -
Antiviral Hospital Textiles:
Singapore’s Temasek Polytech created a copper-ion infused bamboo fabric with 99.9% viral neutralization in 2 minutes (per ASTM E1052-20). Its 3.2 SOM score aids burn patient recovery by minimizing mechanical irritation.
The Future Frontier: As neuromorphic engineering advances, researchers at ETH Zürich are prototyping fabrics with embedded memristors that "learn" individual pressure preferences. Early prototypes adjust fiber stiffness in real-time using 0.1W power, potentially redefining personalized comfort.
The trillion-dollar question remains: Can the textile industry reconcile the thermodynamic paradox of creating materials that feel like warm breath against skin, yet withstand industrial laundering, cosmic radiation, and enzymatic decomposition? With annual R&D investments exceeding $23 billion in smart textiles alone, the answer may reshape not just what we wear, but how we define human-machine symbiosis.
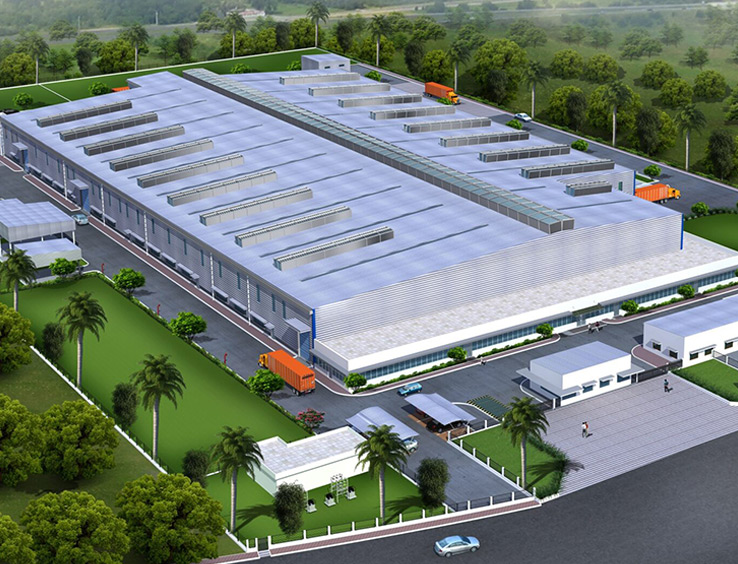
Huzhou Colorful Textile Co., Ltd.
Huzhou Colorful Textile Co., Ltd. is located in Zhili Town High-tech Industrial Park, China's children's wear city. The main production and sales of plush warp-knitted products: for children's clothing spandex super soft and ollie velvet products, compared with the market has obvious cost performance. Due to the reduction of layers of intermediate links, completely control the price advantage. The company has superior geographical location, strict internal management, stable quality (with export orders of professional technical team), hot pillow service, the preferred supplier for garment enterprises cooperation.
More About Us